Pool Professionals
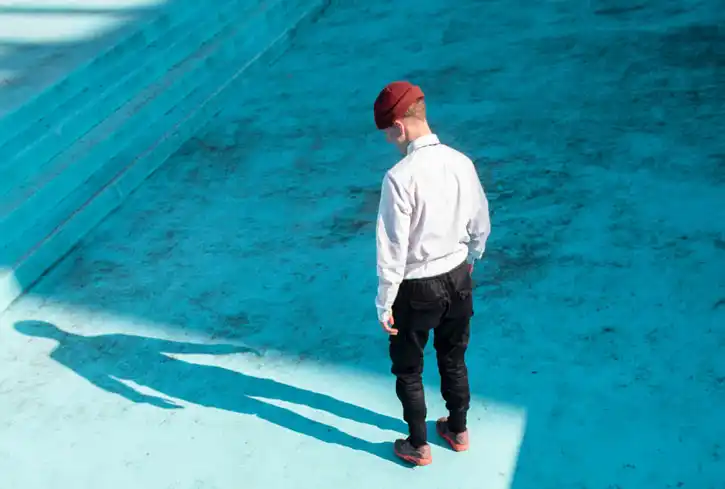
Swimming Pool Interior Finishes & Chemical Etching Deterioration
Swimming pool cementitious finishes are one of the most popular types of in-ground pool surface coatings because of the beauty and durability. There will be more noticeable cosmetic irregularities with smooth trowel finishes, as opposed to exposed aggregate finishes, as the surface interacts with its environment. In order to properly minimize all potential etching problems it takes a combination of good materials, application practices, good start-up procedures and a proper regimen of care and maintenance.
Materials and Water Chemistry
A typical swimming pool cementitious surface coating consists of a mixture of hydraulic cement (typically white), white sands (typically limestone, quartz or dolomite), or other aggregates (colored quartz, pebble, glassbead), water, with or without additives (which aid in the placement and finishing of the cementitious surface), and pigments.1 The principle compounds of white cement prior to mixing with water are: tri-calcium silicate, di-calcium silicate, and tri-calcium aluminate. When white cement is mixed with water, these principle compounds hydrate (react with water) to form an interlocking network of calcium silicate hydrate (CSH) and calcium alumino-silicate hydrate (CASH), which are the principles ‘binders’ of hardened white cement.2 Simultaneously, the compound calcium hydroxide (CH), which is a more soluble compound, is formed. CH makes up approximately 24-27% of fully-hydrated white cement.


Hard Troweled Surface
Inherent in cementitious coatings are many small void spaces and micro-cracks. There is a special region in cement/aggregate mixtures called the Interfacial Transition Zone (ITZ). These ITZ’s exist at the interface of the cement binder and the aggregates; ITZ’s also exist at the interface of the cement binder to the tile, around lights and/or PVC pipes and other dissimilar materials in the plaster. The chemical and physical properties in the ITZ’s are different from the bulk cement paste in that they contain significant amounts of calcium hydroxide and have a higher water/cement ratio and greater porosity. 3, 4


For swimming pools, water chemistry plays an important role in the life expectancy of a cementitious coating. It is important that the water chemistry is maintained to proper industry standards to maximize the long-term durability and aesthetics of the pool’s interior finish.
However, a cementitious interior finish’s overall life expectancy can be severely reduced whenever water is allowed to be in an aggressive condition for extended periods of time. The term “aggressive pool water” is considered to be water that is chemically outside of established balanced ranges. This aggressive water is capable of removing, dissolving, or otherwise reacting with components of the surface materials causing accelerated deterioration. This would include water that has low calcium hardness, low pH, low carbonate alkalinity, and/or a combination of these. 5


Reactions with the soluble cementitious materials can take place whenever water, or moisture, is allowed to permeate through a cementitious surface coating. Water that is not maintained in the “ideal ranges,” as defined by ANSI/APSP to be “balanced”6, can deteriorate a cementitious surface coating by dissolving components of the cement/aggregate matrix, resulting in the leaching of cement compounds. Leaching generally appears as etched areas on the surface, especially where calcium hydroxide is most abundant. Calcium hydroxide is the most soluble cement compound and is the first compound to be dissolved.
These etched areas are around aggregate particles, tile inserts and other interfaces and often appear as small spots. As with all chemical or physical action on a surface that is capable of removing or dissolving away elements or compounds of that surface, water chemistry will play a key role in the etching process. Low calcium hardness, low carbonate alkalinity, and/or low pH create an aggressive environment that will lead to etching in the areas with the greatest solubility and porosity such as in the ITZ’s. Continued leaching can cause complete dissolution of the cement paste over time in those regions of the coating.7
The pool/spa water pH, carbonate alkalinity, calcium hardness and total dissolved solids, should be frequently monitored and maintained with normal diligence such that the water is in equilibrium.9 Testing should take place one to two times a week for pH, total alkalinity and free/total chlorine and once a month for calcium hardness, stabilizer (cyanuric acid) and TDS. The NPC encourages the use of the Saturation Index as the method to achieve balanced water. While APSP acknowledges an acceptable Saturation Index range of -0.3 to +0.5, they state the ideal range is 0.0 to +0.5. The NPC further refines the ideal range to 0.0 to +0.3. Certain high performance durability finishes can tolerate slightly negative indices for short periods of time.
Mechanism | Potential Deterioration/Issue |
Low Calcium Hardness | Dissolution of calcium compounds; discoloration |
Low pH | General dissolving of materials |
Low Carbonate Alkalinity | Slow dissolution of hydroxide/bicarbonate ions |
High Cyanuric Acid Levels (stabilizer) | Combination of dissolving and leaching; pigment “fade”- low carbonate alkalinity |
Direct physical contact with certain chemical compounds (i.e. sodium chloride, cyanuric acid, granular chlorine products, sodium bisulfate, shock treatments, etc.). |
Discoloration, water entrapment, pigment alteration |
Some chemical compounds in direct contact with interior finishes can cause dissolution or alteration of these pool surfaces. Compounds such as cyanuric acid (stabilizer) and salt (NaCl) can create conditions that will have significant impact on
the Saturation Index calculations. For example, elevated cyanuric acid levels (CYA) will impact the carbonate alkalinity measurement. Remember, only carbonate or adjusted alkalinity can be used to calculate the Saturation Index. Also, with higher
salt levels, the water can be more aggressive.
Conclusions:
Swimming pool interior finishes are designed to provide a serviceable and aesthetically appealing finish to the pool. Therefore, to prevent etching deterioration along with other issues, the most critical care item
is maintaining proper water balance. To optimize the long term durability and appearance of any cementitious interior pool finish, proper materials, proper workmanship and balanced water chemistry must all be present.
References:
- National Plasterers Council, “Technical Manual”, 8th Edition, 2016, pgs. 5 – 8.
- Steven H. Kosmatka, Michelle L. Wilson, “Design and Control of Concrete Mixes”, 15th Edition, 2013, Portland Cement Association, Skokie, IL, pg. 49.
- Adam Neville, “In My Judgement – There is More to Concrete than Cement”, Concrete International Magazine, January, 2013, pgs. 73 – 74.
- Sidney Diamond, “Cement Paste Microstructure in Concrete – Microstructural Development Driving Hydration of Cements”, Materials Research Society, Symposia Proceedings, Vol. 85, pgs. 21 – 31.
- National Plasterers Council, “Technical Manual”, 8th Edition, 2016, page 25.
- ANSI/APSP – 11, “American National Standards for Water Quality for Public Pools and Spas”, Appendix A, Sections A-1 to A-3, 2009.
- National Plasterers Council, “Technical Manual”, 8th Edition, 2016, pgs. 25 – 26.
- ANSI/APSP – 5, “American National Standard for Residential Inground Swimming Pools”, Appendix A,
Sections A-1 to A-3, 2011. - National Plasterers Council, “Technical Manual”, 8th Edition, 2016, pg. 27.
Other General References:
The Association of Pool and Spa Professionals, “Service Tech Manual”, 4th Edition, V. 4.3,
Alexandria, VA, 2013.