Pool Professionals
Swimming Pool
Cementitious Interior Finishes “WATERTIGHT” vs. “WATERPROOF”
The National Plasterer’s Council Technical Manual states that the plastering of a swimming pool when properly mixed, placed, and finished, should create the desired decorative finish that is maintainable and watertight.1 In actuality, the watertightness of a swimming pool is achieved from a combination of the shotcrete or concrete structure and the interior finish coating. While all swimming pools should be watertight, not all swimming pools are waterproof. Moisture and water vapor permeate through the structure of a swimming pool, but liquid water should not.1,2,3 When stipulated, certain swimming pool structures can be made waterproof (or almost waterproof) through special designing and engineering.4,5
The Swimming Pool Structure and Penetrations 1,2,3,7
Most inground swimming pools in the United States are shotcrete (wet or dry concrete mixtures that are shot at high velocity) though there are poured concrete swimming pool structures as well. A good shotcrete structure together with a good interior finish coating should not leak water. While the shotcrete can be engineered and placed in a manner that creates a structure that is watertight, it is an unrealistic expectation that shotcrete will be watertight at penetrations, or where it butts up to a dissimilar material.
Swimming pools are typically shot monolithically, meaning one continuous application, with no relief joints. Therefore, it is normal that some separation will develop around penetrations through the shotcrete structure (plumbing, lights, etc..). This is due to the normal shrinkage that occurs during the setting of the hydraulic cement. While the shotcrete fully encapsulates piping, light niches, and other penetrations, a certain amount of separation around these penetrations is inevitable.
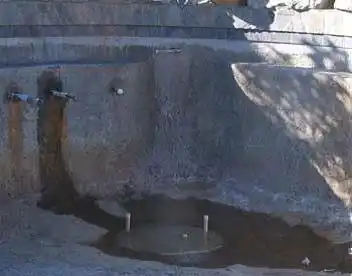
Water intrusion at penetrations from behind the structure prior to application of the interior finish coating
Therefore, all penetrations through the shotcrete need to be sealed or plugged. Interior finishes that are continually troweled through to final set (or hard troweled) are capable of sealing around these penetrations without the need to be pre-sealed. Other interior finishes, where troweling is discontinued prior to the final set, may require that all penetrations be sealed or plugged prior to applying the interior finish coating. It is common practice, to dig out (a.k.a. ‘cup out’ or ‘box out’) the shotcrete around some or all penetrations for this purpose. Typically, dig outs for return lines are a nominal 1 ½” – 2″ in depth by a nominal 3″ – 4″ around the piping. Suction lines require a much larger dig out, depending upon the type of main drain base ring and cover that will be installed.

Plumbing penetrations with fittings and pre-sealed
Dig outs allow better access to the piping, making it easier to cut the pipe far enough back to ensure that fittings will be flush with the anticipated surface of interior finish coating. Dig outs also allow access and space to apply a sealant or plugging material around the penetrations, ensuring they will be watertight. Other penetrations that require no other adjustment or work to be done prior to the application of the interior finish coating may often have little or no dig out. The burden of ensuring that penetrations are sealed and/or plugged may fall to the Builder, Plasterer, or to the Pre-Plaster Prep Crew depending upon which party is given the responsibility. For commercial and public work, the Engineer, Architect, or Designer should stipulate the party responsible for sealing or plugging of all penetrations in a manner that ensures all are watertight.
The following considerations, as to the type of material and method of installation, are suggested for sealing or plugging penetrations:
- The usage of non-shrinking or low-shrinkage cementitious plugging material.
- Non-sanded cementitious materials should be used only as a thin slurry coating within the dig out, as per manufacturer’s recommendations, and should not be used as a method of filling the entire dig out.
- The inclusion of a polymeric fortifier, proven stable under water, with the cementitious plugging material, as per manufacturer’s recommendations.
- The usage of sealants that are not compatible with cementitious materials should be confined to sealing only the immediate area at the interface of the penetration and the shotcrete and should not be used to seal or coat the interior of the dig out, piping, or other fixtures.
- The removal of any loose material or debris and thorough washing around penetrations to ensure a good adhesion bond or ‘keying’ of the interior finish coating with the shotcrete.
- Plugging or filling dig outs flush with the overall shotcrete surface, as opposed to using finish coating material while plastering, may help to prevent differential hydration discoloration caused by the interior finish coatings increased thickness at dig outs.
- Plugging material should be allowed to thoroughly dry and/or cure, as per the manufacturer’s recommendations, prior to applying the interior finish coating.
Sealing of Substrate Cracks
It is imperative that a swimming pool shotcrete mix is designed to restrict the permeation of water. This typically requires that a shotcrete mix design has an adequate amount of cementitious material; a low water:cement ratio; a pozzolan or polymer modifier addition; or some combination of these, to produce a watertight shotcrete. A good shotcrete mix design will reduce the amount and size of shrinkage cracks that develop at the surface. Proper reinforcement, structural design, and proper mixing and placement of the shotcrete materials ensures that the swimming pool structure has no structure cracks. Plastic, autogenous, or shrinkage cracks are visible on the surface of most monolithic shotcrete structures; however, these cracks are plugged and sealed shut by the interior finish coating. However, structural movement cracks can reopen existing cracks or create new cracks after the interior finish application.
Curing of the Substrate
Curing is a method of maintaining adequate moisture within the material near the surface to ensure ongoing hydration of a cementitious binder that may otherwise dry out. This is usually a deliberate action taken, such as misting, soaking, or covering of the surface to maintain an elevated humidity level within the matrix of the material (ideally, this is at or above 85% R.H. within the matrix of the material). As with all shotcrete and concrete structures, proper curing reduces rate and size of shrinkage cracking near the surface. Proper curing also improves the overall strength gain properties, which in turn, imparts watertightness to the swimming pool structure. 1,6
It has been shown that extending wet curing from three days to seven days can result in a 10% – 20% reduction in shrinkage cracking at the upper surface. For shotcrete swimming pool structures that are to receive a cementitious finish coating, the ASA Position Paper ‘Curing of Shotcrete for Swimming Pools’ and the National Plasterer’s Council (NPC) Technical Manual recommends that moist curing be continued for 28 days. Ideally, the first seven days the shotcrete should be soaked three to five times daily, dependent upon the climate or region of the country. Cooler regions or cooler times of the year may require less. This is typically done by spraying water onto the shotcrete surface with a garden hose. 1,6
Installation of the Interior Finish 1
The surface of the interior finish should be placed and finished in such a way that ensures the watertightness of the swimming pool. There should be no open cracks, holes, or gaps at the tile line, rocks, or other transition areas that would allow water to pass freely through the coating. The plaster application should be finished in a way that provides a tight seal around plumbing fixtures, lighting fixtures, and other penetrations through the shotcrete structure.
Though all cementitious interior finishes for swimming pools develop some shrinkage cracking or check cracking prior to the time they are filled with water, these cracks typically reseal themselves once underwater, as the cement binder continues to hydrate underwater. 8, 14, 15
Shotcrete and interior finish coatings are considered semi-permeable membranes. As such, moisture and water vapor permeate through the structure and into soil over time. However, swimming pools are designed to be watertight. Free liquid water should not pass through the structure. Certain placement environments may require a swimming pool to be waterproof (or almost waterproof) and as such, special design and engineering must be stipulated.
Waterproof Structures 4,8-20
This Technical Bulletin is not intended as a resource to explain the materials and application for waterproofing swimming pools. This section is solely intended to show the differences between ‘watertight’ and ‘waterproof’, and to teach the general attributes of both.
Each waterproofing manufacturer promotes their own unique system, to include proprietary materials and unique application procedures; therefore, these systems should be qualified and demonstrated to be applicable for a specific usage based on the individual project and/or placement environment. Ultimately, the waterproofing manufacturer should ensure that their waterproofing system is compatible with all components of the swimming pool that the system affects, as well as ensuring the long-term compatibility of the waterproofing products in swimming pool water and chemicals.
There are many waterproofing systems to choose from.
- Integral-to-Shotcrete (added into the shotcrete mix during application)
- Integral-to-Slurry Coat (added into a slurry coat or scratch coat prior to plastering)
- Integral-to-Interior Finish (added into the interior finish mix during application)
- Membranes (typically a flexible waterproof coating applied to the pool interior)
- Spray-On (negative pressure side)
- Spray-On (positive pressure side)
The following are examples where waterproofing may be necessary and potential considerations are offered.
Construction of a suspended swimming pool (e.g. built on a shelf, pilasters, etc.) or negative edges, where the outside (back side) of the structure will be visible. For some placements, a positive side (interior) waterproofant alone, may not be sufficient for such placements. It may become necessary that the swimming pool structure itself be made waterproof by using an integral waterproofing added to the cementitious material mix design. Optionally, a method to envelope (inside and outside) the structure by applying a waterproof membrane or penetrating waterproofant that waterproofs the entire structure. This includes waterproofing all the way up to the deck (behind the perimeter tile) and on the top of negative edge (infinity edge) walls. Failure to completely waterproof such a structure can result in moisture migration and eventually unsightly efflorescence (salt build-up) exhibiting in areas of the negative pressure side of the structure.
Preventing water from penetrating or accumulating outside the structure (back pressure). Water should not be allowed to gather or pond against the outside of the swimming pool structure. If water accumulates against the negative pressure side (back side) of the swimming pool structure, the pressure gradient can cause a waterproofing membrane, bond coat, or interior finish to debond. This would include water from rain, irrigation, or other source where the water is impeded and not allowed to escape from the immediate area of the swimming pool structure. Even a seasonal rain or leaking irrigation piping can create significant back pressure resulting in the flexing, stretching, and potentially the debonding of the waterproof membrane, bond coat, or interior finish.
Other examples where waterproofing is recommended.
1. Structures that are out of the ground, such as certain fountains or water features, or portions of a pool where the back side of the structure is visible. 2. Structures that are not monolithic, or that share a wall or portion of another structure, such as a building, house, or sunken bar.It is also recommended that pools and spas that are built on a parking garage, multi-story building, home, or similar structure should be built within a waterproof vault, having a drainage system that removes any water seepage, leakage, or overflow away from the structure.
References
[1-7] Watertightness/Penetrations/Curing
- The National Plasterer’s Council, Technical Manual, 9th Edition, 2016
- American Shotcrete Association, Pool and Recreational Committee, Position Paper 4, Watertight Shotcrete for Swimming Pools, info@shotcrete.org
- American Shotcrete Association, Pool and Recreational Committee, Position Paper 6, Forming and Substrates in Pool Shotcrete, info@shotcrete.org
- American Concrete Institute, ACI 515.2R – Guide to Selecting Protective Treatments for Concrete, www.concrete.org
- American Concrete Institute, ACI 365.1R-17 – Report on Service Life Prediction, www.concrete.org
- American Shotcrete Association, Pool and Recreational Committee, Position Paper 7, Curing of Shotcrete for Swimming Pools, info@shotcrete.org
- J. Dongell, Swimming Pool Penetrations, Shotcrete Magazine, Vol. 17, No. 3, Summer, 2015, pp 10 – 11
[8-20] Waterproofing
- A. Johansson-Selander, J. Trägårdh, J. Silfwerbrand, M. Janz, Water Repellent Treatments – “The Importance of Reaching a Sufficient Penetration Depth,” Concrete Under Severe Conditions: Environment and Loading – Proceedings of the 6th International
Conference on Concrete Under Severe Conditions, CONSEC’10, 2010, pp. 1173–1179 - V. Spaeth, J.P. Lecomte, M.P. Delplancke, J. Orlowsky, T. Büttner, “Impact of Silane and Siloxane Based Hydrophobic Powder on Cement-Based Mortar,” Advanced Materials Research 687.100, 2013, pp. 100–106
- P. Reiterman, J. Pazderka, “Crystalline Coating and Its Influence on the Water Transport in Concrete,” Advances in Civil Engineering, Vol. 2016
- J. Pazderka, E. Hájková, “Crystalline Admixtures and Their Effect on Selected Properties of Concrete,” Acta Polytechnica Vol. 56, Issue 4, 2016, pp. 306-311
- V. G. Cappellesso, P. dos Santos, D. Molin, A. Masuero, “Use of Crystalline Waterproofing to Reduce Capillary Porosity in Concrete,” Journal of Building Pathology and Rehabilitation, Vol. 1, Issue 1, 2016, p. 9
- G. Li, X. Huang, J. Lin, X. Jiang, X. Zhang, “Activated Chemicals of Cementitious Capillary Crystalline Waterproofing Materials and Their Self-Healing Behavior,” Construction and Building Materials, March 10, 2019, pp. 36-45
- P.C. Tran, K. Kobayashi, T. Asano, S. Kojima, “Carbonation Proofing Mechanism of Silicate-Based Surface Impregnations,” Journal Advanced Concrete Technology, Vol. 16, Issue 10, 2018, pp. 512-521
- P. Azarsa, R. Gupta, A. Biparva, “Crystalline Waterproofing Admixtures Effects on Self-Healing and Permeability of Concrete,” 1rst International Conference on New Horizons in Civil Engineering, NHICE-01, 2018
- F. Qin, F. Yang, H. Liu, “Waterproof Measures for Swimming Pools: Use of Cement-Based Permeable Crystalline Waterproof Composite Coatings,” Chemical Engineering Transactions, Vol. 59, 2017, pp. 535-540
- A. Biparva, “Integral Crystalline Waterproofing, The Future of Concrete Durability,” Structure Magazine, Vol. 52, Feb. 2015
- L. W. Teng, R. Huang, J. Chen, A. Cheng, H.M. Hsu, “A study of Crystalline Mechanism of Penetration Sealer Materials,” Materials, Vol. 7, Issue 1, 2014, pp. 399-412
- B. Sengupta, A. Chakraborty, “Reduction in Permeability of Concrete, Mortar and Plasters by a Chemical which Retards Water Percolation and Salt Transfer,” WIT Transactions in Built Environments, Vol. 137, 2014, pp. 639-650
- G. Z. Lu, W. X. Zhao, L. J. Zhou, X. J. Ding, “The Analysis on Mechanism and Application of Cementitious Capillary Crystalline Waterproofing Coating,” Proc. of the 2014 International Conference on Mechanics and Civil Engineering, ICMCE-14, 2014